Technology Let Loose: Innovations About Aluminum Casting
Technology Let Loose: Innovations About Aluminum Casting
Blog Article
Check Out the World of Aluminum Casting: Insider Secrets and Techniques
In the realm of manufacturing, light weight aluminum spreading stands as a critical process, vital for the creation of a large variety of products. As we browse through the globe of aluminum spreading, there exists a world of insider secrets and methods that can raise the top quality of the last products and enhance the manufacturing procedure.
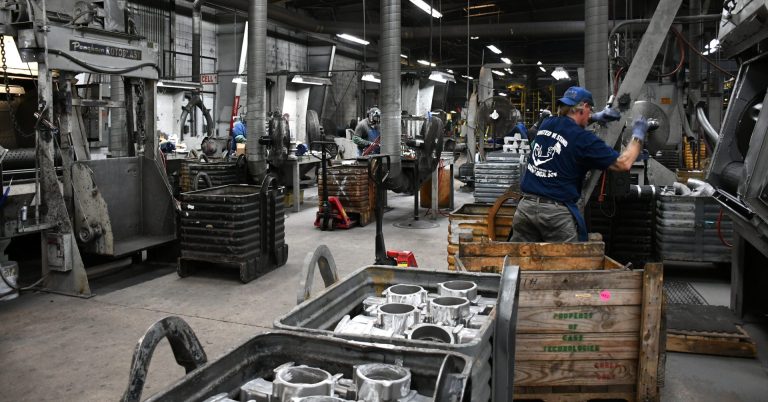
The Basics of Light Weight Aluminum Spreading
Aluminum casting, an essential procedure in manufacturing, involves the putting of liquified light weight aluminum into a mold to attain wanted shapes and structures. This flexible technique is widely made use of throughout numerous industries due to light weight aluminum's outstanding residential or commercial properties such as high strength-to-weight ratio, corrosion resistance, and thermal conductivity.
The procedure begins with the melting of light weight aluminum in a furnace at temperatures surpassing 1220 ° F(660 ° C ) As soon as the aluminum reaches its liquid state, it is poured into a pre-designed mold and mildew tooth cavity. The mold, usually made from products like steel or sand, identifies the last shape of the actors aluminum part.
After pouring, the light weight aluminum is entrusted to solidify and cool down within the mold - about aluminum casting. This cooling period is crucial as it determines the honesty and quality of the end product. When strengthened, the mold is eliminated, disclosing the freshly formed light weight aluminum spreading
Expert Tips for Successful Casting
To achieve optimal cause aluminum casting, careful interest to detail during the mold and mildew layout phase is vital for guaranteeing successful results. One insider tip for successful spreading is to very carefully think about the gating system. The style of the gating system plays a crucial function in regulating the flow of liquified aluminum right into the mold cavity, making sure proper dental filling and minimizing problems like air entrapment. Furthermore, keeping the proper steel temperature level is essential for accomplishing top quality spreadings. Tracking and regulating the metal temperature throughout the spreading process can aid avoid issues such as early solidification or porosity in the end product.
Furthermore, an additional essential suggestion is to correctly prepare the mold surface area. A well-prepared mold and mildew surface area can add to better metal flow, reduced turbulence, and improved surface area finish on the actors component. This preparation may include making use of finishings or treatments to improve mold release and prevent metal/mold interactions that might result in defects. By paying very close attention to these expert suggestions, manufacturers can boost the high quality and efficiency of their aluminum casting processes.
Advanced Strategies in Light Weight Aluminum Spreading
Using ingenious strategies and innovative approaches, the realm of aluminum spreading has seen a significant evolution in the direction of progressed techniques that push the limits of typical methods. One such technique is vacuum cleaner casting, which includes creating a vacuum setting to remove air from the mold tooth cavity, resulting in greater quality and even more detailed castings with lowered porosity. Furthermore, financial investment spreading, additionally recognized as lost-wax casting, is a polished approach that allows for intricate forms and slim walls, leading to thorough and exact aluminum parts.

In addition, advanced simulation software plays a crucial role in maximizing casting layouts and predicting potential issues, enabling changes to be made prior to the actual spreading process starts. By accepting these innovative strategies, manufacturers can raise their light weight aluminum casting capabilities to brand-new heights, fulfilling the needs of contemporary markets with accuracy and development.
Understanding Various Casting Methods
In the world of manufacturing, an extensive understanding of numerous casting methods is vital for accomplishing optimum lead to metal construction processes. Various casting techniques provide one-of-a-kind advantages and are selected based upon aspects such as the complexity of the style, production volume, material requirements, and expense factors to consider. Among one of the most typical spreading approaches is sand spreading, where a mold and mildew is produced using sand as the primary product. Sand spreading is functional, cost-effective, and suitable for generating huge components.
One more prominent spreading method is pass away casting, which includes infusing molten steel into a mold tooth cavity under high stress. By recognizing the nuances of different casting techniques, producers can make educated decisions to enhance their production processes and accomplish the desired Click This Link results.
Optimizing Efficiency in Spreading Operations
With a solid grasp of the nuances of different casting approaches, manufacturers can simplify their procedures to improve performance in steel fabrication processes. Taking full advantage of efficiency in casting procedures needs an organized method that concentrates on optimizing every action of the casting procedure. One key strategy is to carry out lean manufacturing principles to remove waste and enhance total performance. By identifying and removing traffic jams in the manufacturing line, producers can enhance process and decrease lead times.
In addition, purchasing advanced modern technology and tools can substantially enhance performance in casting procedures. Automated systems, robotics, and computer-aided layout (CAD) software can improve procedures, decrease mistakes, and boost outcome. In addition, training workers on the most up to date strategies and finest methods can additionally add to optimizing efficiency in casting procedures.
Regular upkeep of tools and tools is crucial to avoid break downs and lessen downtime - about aluminum casting. Executing an aggressive maintenance routine can aid determine potential problems before they intensify, making sure smooth operations and undisturbed manufacturing. In general, by focusing on performance and constant enhancement, manufacturers can maximize my explanation their casting procedures visit homepage and remain affordable in the market
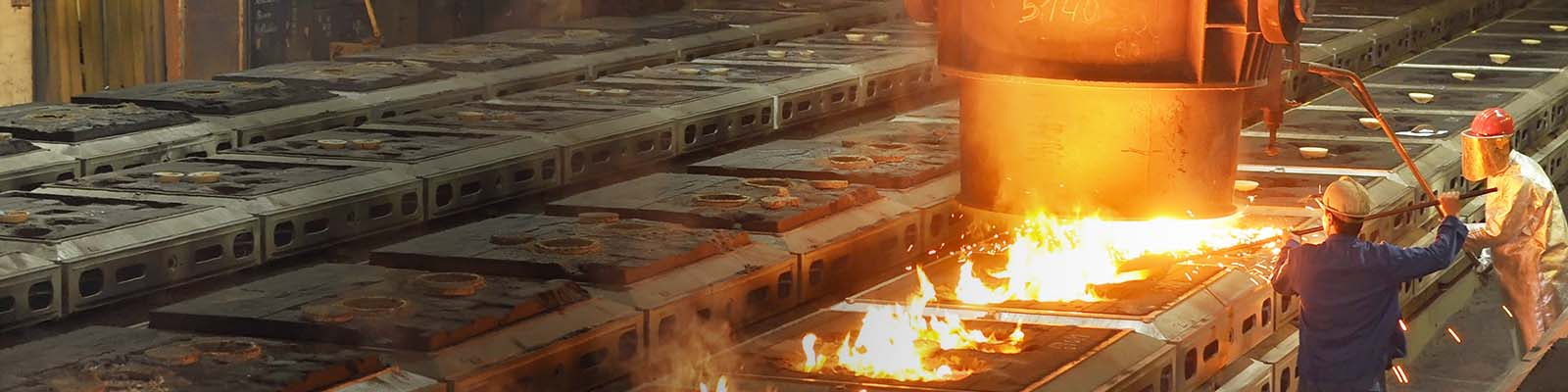
Final Thought
In final thought, the globe of light weight aluminum spreading provides a broad range of opportunities for those looking to create elaborate and resilient metal items. Comprehending the numerous spreading techniques and maximizing performance in operations are vital components to accomplishing top quality results in light weight aluminum casting.
One such method is vacuum casting, which entails creating a vacuum cleaner environment to remove air from the mold and mildew tooth cavity, leading to greater quality and more intricate spreadings with decreased porosity (about aluminum casting). Furthermore, investment casting, likewise understood as lost-wax spreading, is a refined method that permits for thin walls and complicated shapes, resulting in exact and detailed light weight aluminum parts
One of the most typical casting approaches is sand casting, where a mold is produced using sand as the main product.An additional prominent casting approach is pass away casting, which entails infusing liquified steel right into a mold and mildew tooth cavity under high stress. Understanding the different casting methods and maximizing effectiveness in procedures are key components to achieving top notch results in aluminum casting.
Report this page